Our Educate A Child International Fixed Term Deposit empowers education for marginalised and vulnerable children.
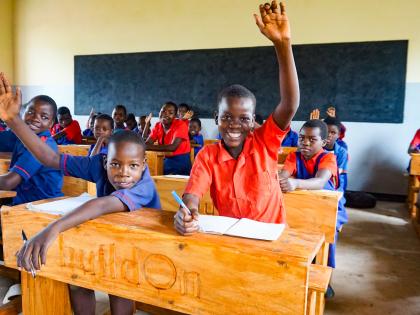
Britain has a long history of coin use and manufacture. We first began importing coins in the Iron Age, around 150BCE, and we started making our own money in about 100BCE. Coin manufacture was largely ended by the Roman occupation; although the British still used coins, they were primarily minted elsewhere in the Empire. The one exception was a single British mint in London that was created at the end of the third century CE and functioned for about 40 years.
It was not until approximately 250 years after the Romans had left Britain that a mint was once again established in London. But minting was not confined to the capital; it is estimated that by the reign of King Aethelred II (978-1016) there were more than 70 mints, primarily in the south of England. However, these numbers dwindled and by the 13th century, minting was mainly confined to London and Canterbury.
In 1279, the mints were unified into one system, The Royal Mint, and operations were moved to the Tower of London, where they remained for the next 500 years. Historically, coins were struck by hand but by the late 1700s, the process became mechanised to keep up with demand and help to foil counterfeiters. When the Tower had to accommodate mills and presses, it became clear that it was just too small. The Royal Mint was moved to near Tower Hill in 1809 and coin manufacture became steam powered the following year. Later that century, steam gave way to electricity and the continual struggle to cope with enormous demand, exacerbated by the forthcoming introduction of completely new decimal coinage in 1971, led to the transfer of the Royal Mint to Llantrisant in 1968. That is where the Mint remains to this day.
Today coin manufacture is a three-step process:
• Making the blanks
• Making the dies
• Striking the coins
Making the blanks
The process begins by taking correct proportions of metal for each coin denomination and melting them in a furnace. A long strip of the mixed metal – or alloy – is produced by the furnace, which is then cut into coils weighing nearly three tonnes.
Rolling mills flatten the coil to the correct coin thickness before a press punches discs from the strip – at a rate of 10,000 a minute. As there is yet no design on the coins, these discs are called ‘blanks’. The blanks are heated up to 950oC to ensure they are not brittle and soft enough to handle the next stage of coin manufacture. They are then cleaned and checked for faults.
Making the dies
The designs on our coins are pressed in using a stamp, or ‘die’. The original coin design is created by an artist, often in plaster, and is much larger than the final coin. The design is then scanned and stored as a digital file.
A machine then engraves the design onto a steel hub, which is then used to create the working dies that will strike the coins. Interestingly, the dies are like a photo negative, so the design is in reverse.
Striking the coins
The final step brings together the above two processes. The blanks are fed into a coining press that contains two dies – one for each side of the coin. The dies strike the blanks 850 times a minute and apply a pressure of approximately 60 tonnes.
The mint then issues the newly minted coins to cash centres, operated on behalf of major banks and post offices. From there, they are distributed to local branches of banks and post offices and ultimately, into our pockets.